|
|
|
|
|

PFLEGE & RESTAURIERUNG
Die "Logo" wird restauriert
von Thorsten Wildies
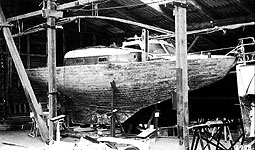
Die Werft brannte, als sie gebaut wurde. Schon am 10. Tag ihres Wasserdaseins brummte sie mit voller Fahrt auf das Vilm-Steinriff. Sie überstand den Bombenterror über Berlin und entkam unbeschadet der Sturmnacht von l989 in Marina Wentorf. Stolze 81 ziemlich bewegte Jahre hat sie durchlebt und kann jetzt bald einem zweiten Segelfrühling entgegensehen: Die "Logo", ein 9,80 m Tourenkreuzer aus der Feder von Arthur Tiller. Vor i 0 Jahren erwarb ich die alte Segelyacht und mit der Zeit wuchs sie mir ans Herz. Viele Jahre intensiver Recherchen waren nötig, um etwas über ihre Geschichte in Erfahrung zu bringen.
Die "Logo" wurde 1922 auf der Werft der Geb. Burmester in Bremen-Burg mit einer Sloop- und Yawl-Takelage mit Steilgaffel gebaut. Sie erhielt einen Zweizylinder Einbaumotor und ein offenes Cockpit, wobei der Kajütaufbau etwas niedriger als der jetzige und vorn halbkreisförmig gebogen war. Die stabile Yacht wurde im Auftrag von Dr. CurtJanssen, einem Rechtsanwalt aus Berlin von der Seglervereinigung 1903 Berlin, entworfen. Wer die Seereiseberichte aus den ersten Jahren mit seiner "U" liest, weiß, dass Janssen ein begeisterter Segler gewesen sein muss. Befand sich der Heimathafen auch in Schwanenwerder am Wannsee, so unternahm das Boot doch schon damals zahlreiche Reisen auf den Berliner Gewässern und auf der Ostsee. "Ein unvergesslicher Kindheitstraum, der uns wehmütig das ganze Leben begleitete", schrieb mir im Rahmen meiner Recherchen die Eigner-Tochter Rosemarie Janssen, die kaum glauben konnte, dass es ihre "Li" noch immer gibt. Nur schweren Herzens gab CurtJanssen die Yacht auf, nachdem sie 1945 von den Amerikanern beschlagnahmt worden war.
Auch nach dem II. Weltkrieg blieb die "Li" unter den Namen "Passat" in Berlin beheimatet. Das Boot wurde in den 50ern generalüberholt, erhielt eine neue Kajüte, ein selbstlenzendes Cockpit und ein Hochrigg. Sie ging durch mehrere Hände, bis sie als "Fantasie" 1975 im Hamburger Yachthafen in Wedel als Weltumsegler zum Verkauf angeboten wurde. Die Yacht war inzwischen mit GFK überzogen, gelb gestrichen und hatte vier Holzkisten für Fender und Leinen auf Vor- und Achterdeck sowie einen Außenborder am Heck. Ihre Seereling erinnerte an eine chinesische Dschunke und ihr damaliger Eigner soll viel über Boot und die Welt berichtet haben, was damals aber so niemanden wirklich interessierte, hörte sich alles doch eher wie ein Abenteuerroman an... Anschließend segelte eine junge Familie mit der "Logo" vorwiegend auf der Ostsee, bis ich das Boot 1990 erwarb und Reisen auf Elbe und Ostsee unternahm, die das Boot bis zu den Alandinseln brachten. Der wahre Zustand des Schiffes war aufgrund des "Leichenhemdes" schwer einzuschätzen. Ich sah nur zwei Alternativen: das Boot segeln bis es auseinander fällt oder eine aufwendige komplett Sanierung. Ich entschloss mich für das letztere. Man muss sich schon in das Boot verliebt haben und zugleich etwas verrückt sein, um sich soviel Arbeit aufzubürden. Ich werde häufig gefragt, ob ein Neubau nicht schneller und einfacher gewesen wäre. Das kann schon sein. Nur stellte sich für mich diese Frage nie. Mir ging es darum, dieses Boot zu erhalten auch wenn durch die Restaurierung alte Substanz raus muss, bleibt doch mehr erhalten als wenn man sie abgewrackt hätte. Die Restaurierung begann im Herbst 1997 und vielleicht, ganz vielleicht kommt die "Logo" noch in diesem Sommer wieder ins Wasser.
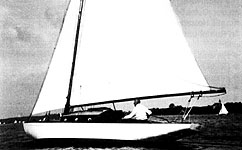
Die 'Li" in der 20er Jahren wohl auf dem Wannsee. L: 9,82 m, B: 2.4 m. T: l ,35 m, Segelf.:48 qm, Verdr.: 4 t
Das "Leichenhemd" muss runter
Das Boot erhielt in den sechziger Jahren einen Kunststoffüberzug von ca. 5 mm Stärke. Mein Voreigner musste ihn bereits im Kielbereich erneuern, da er sich vom Untergrund gelöst hatte. Nach 10 Jahren hatte sich das GFK erneut abgelöst und das auch an anderen Stellen wie Heck, Püttinge und unterhalb der Scheuerleiste. Die Ungewissheit, wie es wohl darunter aussehen möge, ließ mir keine Ruhe, daher entschloss ich mich, das Leichenhemd komplett abzureißen. Im Kielbereich, wo es lose war, konnte man es leicht mit einem Holzkeil anlüften und mit dem Stecheisen großflächig abtrennen, ohne den Untergrund zu beschädigen. Es liefen mindestens 5 Liter Wasser aus den Zwischenraum. Aber auf der Außenhaut saß es doch noch besser als gedacht. Ich vergab die Arbeit an eine Werft. Man entschloss sich mit einer Säge horizontale und vertikale Schnitte im Abstand von 5 cm zu machen und die einzelnen Parzellen mit dem Stecheisen abzuschlagen. Eine üble Arbeit, bei der es sich nicht vermeiden ließ, dass hin und wieder Säge oder Stecheisen im Holz landeten. Noch unangenehmer war das Abschleifen der Glasfaserreste. Das ganze Boot war trotz Abklebens innen mit den feinen Fasern bedeckt. Es wurde nur grob geschliffen, da das Boot vor dem Überziehen stark ausgetrocknet war und die Planken sich nach außen geworfen hatten sowie einige Planken nicht mehr an den Spanten anlagen. Beim Erneuern der Spanten entstanden so Absätze. Trotz der z.T. großflächigen Ablösungen waren kaum rotte Stellen zu entdecken. Nur der Spiegel war von außen verrottet, da durch den unzureichend abgedichteten Heckkorb Wasser eindrang. Der Überzug war auch von Osmose befallen. Es hatten sich mit Wasser gefüllte Bläschen von 1/2 Zentimeter gebildet. Vor dem Überziehen muss das Boot austrocknen, damit der Polyesterharz sich gut im Holz verankern kann. Die entstandenen breiten Plankennähte wurden mit Spachtelmasse ausgefüllt, um dem Rumpf wieder Festigkeit zu geben. Da ein Boot ja nicht gänzlich trocken zu halten ist und die Planken von innen nur geölt sind, konnten die Planken wieder quellen, was meiner Meinung nach dazu führte, dass viele Spanten gebrochen sind.
Die Reparatur der Spanten
Es gibt mehrere Möglichkeiten gebrochene Spanten zu reparieren. Z.B.: Hilfsspanten daneben setzen, bei der Bruchstelle neue Stücken einschäften oder das gesamte Spant auswechseln. Dies macht Sinn, wenn es bereits mehrfach gebrochen oder angefault ist. Man kann nun die Spanten lamellieren, das heißt aus mehreren Schichten verleimen oder einbiegen. Bei dem lamellierten Spant muss erst ein Modell angefertigt werden, das Spant möglichst genau verleimt und anschließend die Schmiege angepasst werden. Dies kann ein bisschen dauern, wenn es gut sitzen soll. Die klassische Methode ist das Einbiegen gedämpfter Spanten, die ich klar favorisiere, da sie ein paar Vorteile bietet. Die weichen Spanten schmiegten sich genau den Planken an und mit etwas Übung kann man bei guter Vorbereitung etwa alle 15 min ein neues einbiegen. Gerade die sorgfältige Vorbereitung macht am meisten Arbeit. Die alten Spanten müssen ausgebaut werden, ohne die Beplankung zu beschädigen. Meist haben wir die Spanten längs mit dem Stecheisen aufgespaltet und nach dem Freipulen der Proppenlöcher die alten Nieten nach außen geschlagen. Dabei sollte man vorsichtig vorgehen, da sonst um den Proppenlöchern das Holz wegsplittern kann, besonders wenn der Nietkopf nicht ganz frei liegt oder schief in der Planke sitzt.
Was braucht man? Eine Wärmequelle, Kessel und Holzkiste. Die Wärmequelle kann ein Ofen, ein offenes Feuer oder eine elektrische Wärmeplatte sein - Je nach den örtlichen Bedingungen. Der Kessel sollte dem Wasserbedarf angepasst sein. Der Wasserbedarf richtet sich nach der Größe der Dampfkiste und der Dämpfzeit. Wir brauchten für 4 Spanten etwa 20 Liter. Ein Nachfüllen ist ungünstig, da sich erst wieder der Druck aufbauen muss und sich somit die Dämpfzeit verlängert. Die Dampfkiste sollte der Größe der Spanten angepasst sein, so dass 4 -6 Spanten hinein passen. Die Dämpfzeit für Eiche beträgt Je Zoll l Stunde. Bei starken Krümmungen bis zu zwei Stunden. Aber dies hängt auch entscheidend von der Holzfeuchte ab. Generell sollte man grünes, frisch geschlagenes Holz verwenden und es feucht lagern. Trockenes Holz ist ungeeignet. Es lässt sich schwer biegen und bricht leicht. Bei starken Krümmungen ist es zu empfehlen, das Spant längs mit der Bandsäge einzusägen.
Ein paar Tipps:
Praktisch ist es, den frisch eingebogenen Spant mit Spax Schrauben zu fixieren, es lässt sich gut ranziehen und spaltet nicht. Wenn das Spant doch nicht so gut passt oder weggelaufen, ist sind die Schrauben mit den Akkuschrauber auch schnell wieder draußen. Früher hat man gleich die Kupfernägel durch die weichen Spanten getrieben. Aber hierbei besteht die Gefahr, das die Spanten aufspalten. Wir haben die Spanten erst mal mit Schrauben fixiert und nach dem Erkalten wieder ausgebaut, geschliffen, geölt und eingesetzt und mit Kupfernägeln vernietet. Die Dämpfzeit beginnt sobald tüchtig Dampf aus der Kiste entweicht. Bei Booten mit S-Spant sollte man im unteren S-Schlag von außen eine Stütze setzen, sonst könnte beim Einbiegen die Beplankung nach außen gedrückt werden.
Vorgang:
Ein Mann befindet sich im Boot, der andere zieht das weiche Spant aus der Dampfkiste und steckt es, wenn das Schandeck entfernt ist, von oben zwischen
Planke und Balkweger.
Bei vorhandenem Schandeck oder wenn die stärkste Krümmung des Spants nahe am Balkweger liegt, muss das Spant von innen hinter den Balkweger geschoben werden.
Im ersten Fall wird das Spant mit einer Schraubzwinge am Balkweger gesichert und mit einem schweren Hammer hineingetrieben, bis es an der Bodenwrange anstößt. Aber nicht zu stark schlagen, sonst hebt es sich beim unteren S.-Schlag wieder ab, auch darf es nicht seitlich ausbrechen. Die Schraubzwinge verhindert ein Zurückrutschen. Der Mann im Boot muss darauf achten, das sich das Spant in der richtigen Position befindet und überall gut anliegt. Sitzt das Spant, werden von außen die Schrauben reingedreht.
Da man ca. nur 4 Minuten Zeit hat, muss alles gut vorbereitet sein. Z.B. Klötzchen zum Nachbarspant und Latten um ihn gegebenenfalls in die gewünschte Lage zu stemmen. Auf diese Weise haben wir 50 Spanten ausgewechselt.
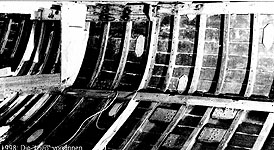
1998: Logo von innen
Wrangen und Bolzen: Die Stahlarbeiten
Rund ums Boot waren eine Menge verschiedenster Stahlarbeiten zu erledigen. Beginnen möchte ich mit den Bodenwrangen. Wie in den zwanziger Jahren üblich wurden die Bodenwrangen aus geschmiedetem Stahl gefertigt, feuerverzinkt und mit Eisennieten vernietet. In der Logo bestehen sie aus 30 X 10 mm Flachstahl, wobei die Enden jeweils fein ausgeschmiedet sind. Alle Wrangen waren mehr oder weniger stark verrostet, die meisten brauchten jedoch nur neu verzinkt zu werden. Aber vier Bodenwrangen aus der Mittschiffsbilge waren so stark vom Rost zerfressen, dass Teilbereiche ausgetauscht werden mussten. Von den ursprünglich 10 mm waren nur noch l bis 2 mm übrig geblieben.
Die verrosteten Teile wurden mit der Hex abgetrennt und durch neue Stahlwrangen ersetzt. Bei Lochfraß oder bei zu dünnen Stellen wurde neues Material aufgeschweißt.
Dabei sind einige Punkte beim Schweißen zu beachten. Die Art der Elektrode muss zum Stahl passen. Dies war besonders beim Überholen der alten Bodenwrangen wichtig, denn hier handelte es sich noch um Puddeleisen. Dies ist ein gut schmiedbares Eisen. Hier ist die mittelstark ummantelte Elektrode MSU Fox von Böhler einsetzbar. Deckt sie doch den Bereich der Stähle von St 32 bis 42 gut ab. Dies war auch bei Auftragsschweißungen der Rostlunker wichtig. Einige Bodenwrangen mussten nach Modell neu gebaut werden. Waren die alten noch aus einem Stück geschmiedet, wurden nun die neuen aus mehreren Eisenteilen zusammengeschweißt. Wichtig ist hier die Schweißnahtvorbereitung. Als Material wurde Flacheisen 30 x 10 mm verwendet. Auch hier kam die MSU Elektrode 3,5 mm zum Einsatz. Da aufgrund der Bauform Spannungen in den Nähten auftreten können, ließen wir die Bodenwrangen langsam abkühlen. Wir befreiten sie von Rost und Farbe mit Hilfe eines Trennschleifers (Flex). Ein Nacharbeiten mit Feile und Drahtbürste ist unerlässlich, um letzte Farbreste aus unzugänglichen Bereichen oder Vertiefungen zu entfernen.
Alle Bodenwrangen wurden neu verzinkt. Die Bohrungen sollten etwas größer sein als für die Bolzen notwendig, damit noch etwas Zink in der Bohrung verbleibt. Denn meist sind die Bohrungen nach dem Verzinken mit Zink zugelaufen und müssen aufgebohrt werden. Auch treten häufig kleine Piken auf, die mit der Feile entfernt werden sollten. Die Oberfläche sollte schimmernde Rechtecke aufweisen. Ist der Zink matt .wurde zu kalt verzinkt. Dies kann besonders bei massiveren Teilen auftreten, wenn sie nicht lang genug im Zinkbad verbleiben.
In der Mitschiffsbilge waren die Wrangen je nach Position mit zwei bis drei Bolzen mit dem Holzkiel verbunden. Alle Bolzen waren leicht bis stark verrostet und mussten zur Sicherheit komplett ausgetauscht werden. Beim Bau hatte man sie von unten durch den Kiel gesteckt. Dies bedeutete, dass wir zuerst den Ballastkiel und das Totholz abnehmen mussten, um die Bolzen rausschlagen zu können. Mit genügender "Überzeugungskraft" (2,5 kg Hammer) kamen alle Bolzen raus. Um dem Boot nicht zu viel an Stabilität zu nehmen, wurden die Wrangen nach und nach ausgebaut, überarbeitet, neu verzinkt und wieder eingebaut. Da das Auswechseln der Bolzen so aufwendig ist, entschlossen wir uns, sie aus Edelstahl zu bauen, damit sie länger halten. Sie bekamen einen quadratischen Kopf von ca. 3x3 cm und wurden in den Kiel eingelassen.
Das Boot hatte nachträglich zwei Stahlspanten und Bodenwrangen erhalten. Auch diese mussten ausgebaut und neu verzinkt werden. In Bilgenbereich wurden Verstärkungswinkel angebracht.
Bau der Bolzen:
Die alten Bolzen waren aus verzinktem Stahl, aber so stark verrostet, dass alle ausgewechselt werden mussten. Insgesamt ca. 100 Stück in den Durchmessern von 8, 10, 12 und 16 mmn sowie die Kielbolzen 24mm wurden erneuert. Verwendet wurde Edelstahl (V2A). Auf einem Ende der Stange wurde das Gewinde für die Mutter geschnitten. Als Kopf wurde ein Stück Flach Niro 30 X 30 oder 20 X 20 angeschweißt. Aus Festigkeitsgründen wurde der Kopf durchgebohrt, die Stange durchgesteckt und von beiden Seiten verschweißt. Es mussten 50 Bodenwrangen ausgebaut, überarbeitet, verzinkt und wieder eingebaut werden. Somit wurden alle Verbindungsbolzen im Rumpf erneuert.
Da die Bolzen auch für die verzinkten Bodenwrangen verwendet wurden, macht uns der Spannungsübergang zwischen verz. Stahl und Edelstahl Sorgen. Hier heißt es, beide Teile durch Dichtmaterial, Fett oder ähnliches abzuschirmen. Denn mit Seewasser in der Bilge eines Oldtimers ist immer zu rechnen.
Ein unbehagliches Thema: Die Kielbolzen
Für alle Eigner alter Boote ist das Thema Kielbolzen immer mit Unbehagen verbunden. Auch wir wussten nicht, was uns erwarten würde. Die Bolzen und Muttern in der Bilge sahen aber noch gut aus. Nach dem Ausbauen zeigte sich, dass sie wohl noch lange gehalten hätten. Ich nehme an, sie wurden schon einmal in den sechziger Jahren ausgetauscht. Sie waren l Zoll stark. Die neuen sollten aus Edelstahl sein (M 24). Sie wurden mit viel Dichtmasse (dauerelastischer Betum-spachtel) eingesetzt. Zum einen, um die Luft in der Bohrung zu füllen, zum anderen, um den Edelstahlbolzen vom Gusseisenkiel zu isolieren. Wir hatten Glück und konnten die alten Bolzen als Muster verwenden. Das Nachmessen ist aber unverzichtbar. Bei den M 16 und M24 Bolzen wurde das Gewinde mit der Drehbank geschnitten. Dabei kann das Gewinde ruhig etwas länger sein. Hier unser Dank an die Helfer im Hafenstore.
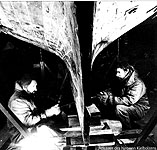
Absägen der hinteren Kielbolzen
Verbindungen aus verschiedenen Metallen sind immer korrosionsanfällig und sollten vermieden werden. Aber Theorie und Praxis sind bekanntlich zwei paar Schuhe. So wird bereits in der alten Literatur dringend davor gewarnt, Bauteile aus verzinktem Stahl mit Kupfernieten zu befestigen. Aber gerade dies wurde bei der "Logo" häufig angewandt. Zum Beispiel beim Ruderkoker. Auch nach fast 80 Jahren war dort keine Korrosion. Die Plankenstöße waren - wie damals üblich - von der Werft aus mit Blechlaschen versehen, und mit Kupfernieten an den Planken vernietet.
Aufgrund unzureichender Befestigung der Decksbalken im Bereich des Brückendecks mussten vier neue Decksknie eingebaut werden. Damit die Knie optisch zu den alten passten, schmiedeten wir die Enden aus. Die Knie schweißten wir aus je zwei Teilen zusammen. Zur Verstärkung wurde noch ein kurzer Quersteg angeschweißt. Nach dem Verzinken wurden sie mit M 6 Bolzen verschraubt. Wichtig ist ein Füllklotz zwischen dem Knie und den Planken anzubringen.
Sämtliche Beschläge , die nicht mehr vorhanden waren, wurden aus verzinktem Stahl nachgebaut. Um dem Baustil und dem Alter des Bootes gerecht zu werden, sollte auf Edelstahl an Deck und Rigg verzichtet werden. Edelstahl wurde nur für die Verbindungsbolzen im Rumpf und für den Ruderkoker verwendet, da der Ruderschaft bereits aus Edelstahl vom Voreigner neu angefertigt worden war. Folgende Beschläge mussten neu gebaut werden: Gaffelschuh, Saling, Topbeschlag, Großbaumbeschlag, Decksaugen für die Dirk, Leitbügel für die Baumfock.
Der Kielbereich: Ein Glücksspiel
Als das GFK entfernt war, zeigte sich, dass das Totholz sehr nass und in Längsrichtung gespalten war. Um die Bolzen für die Bodenwrangen austauschen zu können, musste der Kiel und das Totholz ab. Da wir beim Ausbauen des Totholzes das achtere Fallholz entfernen mussten, setzten wir eine kräftige Heckstütze und vergrößerten die Auflager an den achteren Stützen. Zuerst versuchten wir, die Kielbolzen (M 16) vom Totholz mit einem schweren Hammer raus zu schlagen, aber es rührte sich nichts. Mit einem langen Eisensägeblatt sägten wir zu zweit zwischen den l. und Z. Totholzklotz vom Holzkiel aus gesehen die Kielbolzen durch. Dies dauerte wohl ein paar Stunden, war schweißtreibend aber schonend für das Boot. Nach dem Durchtrennen von drei Bolzen konnten wir das Totholz bestehend aus 4 Klötzen abnehmen und auf dem Hallenboden mit schwerem Geschirr aus einander schlagen - ohne sich Sorgen ums Schiff machen zu müssen. Die Bolzen entpuppten sich als Gewindestangen. Aufgrund des Gewindes saßen sie sehr fest im Holz. Das Totholz (hartes Tropenholz) selbst war gesund. Die Längsrisse brauchten nur geleimt werden. Zum Teil mussten noch Füllklötze eingesetzt werden.
Ernüchtert stellten wir fest, dass der Achtersteven von innen verrottet war. Wir wollten ihn als Modell verwenden und möglichst in einem Stück ausbauen. Zuerst wurden die Verbindungsbolzen zum Kiel gelöst und rausgetrieben. Anschließend lösten wir die Plankenenden von der Sponung und den nächsten Spanten, um sie vorsichtig nach außen drücken zu können, damit der Achtersteven nach hinten rausgezogen werden konnte. Sein vorderer Teil ist breiter als der hintere. Von drinnen konnten wir ihn zwar rausschlagen, aber er war schon zu rott, so dass mehrere Teile abbrachen. Nun konnten wir von unten auf den Heckbalken blicken. Leider war auch dieser in dem Bereich, wo der Achtersteven saß. verrottet. Mit einer langen Schäftung, die genau im Bereich der Kokerbohrung lag. setzten wir ein neues Stück ein. Nun konnte der neue Achtersteven eingepasst werden. Er bestand nun aus zwei Teilen und nicht wie der Alte aus einem Stück. Die Teile wurden so zusammengefügt, dass die Schäftung innen lag. Es war ein endloses Messen, Bearbeiten, Nachmessen und Nacharbeiten. Viele Male musste er ein und wieder aus gebaut werden. Interessant waren dann noch die Bohrungen für die Kielbolzen. Ihre Ausgänge im Kiel und Heckbalken bzw. Bodenwrangen waren vorgegeben Die Bohrungen selbst waren aber nicht gerade. So mussten wir von zwei Seiten in den Achtersteven bohren und hoffen, dass sich die Bohrkanäle in der Mitte treffen würden. Das glich einem Glücksspiel, da die Bohrungen bis zu 60 cm lang waren. Das schafft auch nur eine kräftig Bohrmaschine, die schon beim Bau der Heike III 1962 im Einsatz war. Aber es klappte. Da die Bohrungen krumm liefen, mussten auch die neuen Bolzen krumm geschlagen werden. Wir nahmen V2A M 16 Bolzen mit angeschweißter Platte. Wo sie aus Platzmangel von oben eingesetzt werden mussten, verwendeten wir Bolzen mit beidseitigem Gewinde.
Als der Achtersteven wieder eingesetzt war und die Planken auch wieder in die Sponung passten, konnten wir an die Bohrung für den Ruderkoker denken. Dies ist ein Loch 42 mm Durchmesser, ca. 35 cm lang wird in einem Winkel von ca. 45 Grad gebohrt. Aus einem alten Rohr wurde ein Bohrer gebaut. Am Ende wurde mit der Flex ein Sägezahn ausgearbeitet. Ein Loch war ja im Deck das zweite wurde knapp über dem Heckbalken angebracht, so dass der Bohrer nicht wegrutschen konnte. Eine kleine Bohrung von 12 mm zeigte uns. dass wir richtig lagen. Zu Zweit brauchten wir eine Stunde, um das Loch von Hand zu Bohren. Es passte genau. Welch ein Erfolgserlebnis.
Mittlerweile waren die Bodenwrangen im Bereich des Totholzes schon überarbeitet und der Ballast, ca. l ,5 Tonnen Gusseisen, musste ab. Zuerst wurden mit dem 5 kg Hammer vier l Zoll und zwei 16 mm Bolzen rausgetrieben. Das ging besser als erwartet. Das Boot wurde nun zusätzlich am Bug mit einem Bock abgepallt. Mit Hilfe von drei Winschen konnten wir den Kiel Zentimeter für Zentimeter ablassen. Durch die Form des Ballastkiels vermuteten wir den Schwerpunkt im oberen Teil. Um ein Kippen zu verhindern, ließen wir ihn achtern in einer Kette hängen, die an einem kräftigen Rohr befestigt war, welches wiederum auf zwei Winschen zu liegen kam.
Gleichzeitig wurde beim Ablassen der Kiel zum Boot hin mit einem Keil bzw. Pallholz im Verschlag gehalten. Diese Arbeit sollte in aller Ruhe erfolgen, damit ja kein Unglück passiert. Am Ende lag der Ballast ca. 20 cm unter dem Boot. Nun konnten die Bodenwrangenbolzen ausgebaut werden.
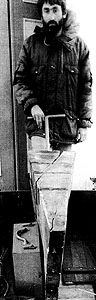
Peter Bock mit dem Totholz
Mit einem Gabelstapler wurde der Ballast unterm Boot hervor geholt, zum Sandstrahlen gebracht und wieder unter dem Boot abgesetzt. Er bekam sechs Anstriche Teerepoxi. Zwischen Kiel und Ballast legten wir Teerfilz und dichteten die Kanten und Bodenwrangenbolzen mit Bitumdichtmasse ab. Beim Anbringen wurde der Ballast wieder mit drei Winden Stück für Stück in die richtige Position gebracht, bis schließlich die Kielbolzen durchgesteckt werden konnten. Anschließend kam das Totholz wieder drunter. Auch hier mussten wir die neuen Bolzen etwas krumm schlagen, damit sie reinpassten. Am Ende sah das Boot schon wieder etwas mehr nach einer Segelyacht aus. Ein wichtiger und umfangreicher Bauabschnitt war nun abgeschlossen.
Die Planken und der Spiegel
Die Dicke der Außenhaut liegt für Yachten der zwanziger Jahre bis 9 m Länge bei l 6 mm, bis II m bei 18 mm und bis 13m bei 20 mm. Das Holz muss lufttrocken, astfrei, feinädrig mit stehenden Jahresringen sein. Nur bestimmte Holzarten eignen sich für Planken z.B. Lärche, Kiefer, Eiche, Mahagoni, Teak oder Kambala. Das Aufplanken einer karweelen Außenhaut kann nach verschiedenen Methoden erfolgen.
Französische Methode:
Ausgehend vom Kiel und Schergang wird jede zweite Planke angebracht. Die
fehlende Planke, auch Stopper genannt, wird später eingekeilt. Deutsche Methode:
Die Planken werden vom Kielgang beginnend nacheinander angebracht, zuletzt
der Schergang.
Entfernung der Stöße voneinander:
Befinden sich zwei Stöße in nebeneinander liegenden Gängen, sollte sie nicht weniger als l -1,5 m auseinander liegen, je nach Bootsgröße. Liegt ein Plankengang dazwischen, so kann die Entfernung 40 bis 90 cm betragen. Zwei Plankenstöße sollten erst dann übereinander liegen, wenn drei Plankengänge zwischen ihnen liegen.
Traditionell werden die Planken stumpf aneinander gestoßen und von innen mit einer Lasche versehen. Meist werden Holzbrettchen, die aus dem gleichen Holz, aus dem auch die Planken bestehen, verwendet. Sie sollten genügend Platz zum Spant haben, damit Wasser ablaufen kann. Bei Yachten aus den 20iger Jahren wie auch der Logo wurden die Laschen auch aus Blechen gefertigt, verzinkt und mit Kupfernägeln vernietet. Sie wurden zusätzlich noch mit den Nachbarplanken verbunden.
Dichten der Plankennähte:
Die Planken sollten an der Innenkante vollständig dicht auf einander passen. aber außen einen kleinen Zwischenraum haben, um die Dichtung (Baumwollfäden) aufzunehmen. In die Fugen wird Baumwolle gedrückt und anschließend verkittet. Zu starkes Eintreiben jagt die Planken auseinander. Befindet sich zu wenig Baumwolle zwischen den Fugen, wird Wasser eindringen. Bei dünnen Planken (Jollen) bis ca. 10 mm werden feine Vertiefungen ins Holz gedrückt, in die später ein Baumwollfaden gelegt wird.
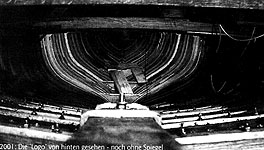
2001: Die Logo von achtern gesehen, noch ohne Spiegel
Die Verhältnisse bei der Logo
Das Boot wurde 1922 aus festen amerikanischem Mahagoni aufgeplankt. Es ist ein sehr hartes, beständiges, aber drehwüchsiges Holz mit lebendiger Maserung. Die alten Nieten waren 2.8 mm stark, ihre Köpfe nur 8 mm im Durchmesser. In der Außenhaut waren sie mit braunen, im Unterwasserschiff mit weißem Kitt zu gespachtelt. Dies spricht für einen ehemals in Natur lackierten Rumpf. Es würde auch erklären, warum sie über Wasser nur noch l 5 mm stark sind. Aber wenn man bedenkt, dass das Boot ursprünglich eine Plankenstärke von 18 mm hatte, ca. alle 7 Jahre abgezogen wurde und dabei schnell ein halber Millimeter draufgeht, sind 3mm gar nicht so viel. Im Vor und Achterschiff wurde sehr viel an den Planken rumgeflickt. Im Extremfall befinden sich auf 2m Plankenlänge drei Stöße.
Die Planken
Als Schergang bezeichnet man die oberste Planke der Außenhaut, Da sie mit den Spanten, Balkweger und Schandeck verbunden ist, wird sie an zahlreichen Stellen von Nieten, Nägeln und Bolzen durchlöchert. Da das gesamte Deck und die Kajüte auf den Balkweger lastet, ist ein Auswechseln des Scherganges immer aufwendig. Das Boot hat im Mastbereich, am Brückendeck und Achtern eiserne Deckskniee, so dass wir nach Entfernung des Scherganges ein Absenken des Decks nicht befürchten mussten. Trotzdem befestigten wir den Balkweger mit Schrauben provisorisch an den Spanten. Um einen sauberen Anschluss zu bekommen, fuhren wir mit der Handkreissäge an der zweiten Planke entlang. Die neue Planke (Sipo-Mahagoni) wurde aus drei Teilen zusammengeleimt. Aufgrund der zahlreichen Plankenstöße entschlossen wir uns die neuen Stöße zu schatten und zu verleimen. Als Muster diente die alte Planke.
Schwieriger waren die Planken im Rumpf, da diese ja an beiden Seiten genau eingepasst sein müssen. Mit einen Hilfsbrett (Ree) und kleinen Klötzchen, die auf das Ree genagelt und an die Nachbarplanken stießen, erhielten wir ein Modell der zu ersetzenden Planke. Anschließend musste sie nur noch ausgesägt und eingepasst werden. Einige Planken müssen sich, um der Rumpfform zu folgen, stark verdrehen. Entweder kann man diese Planken unter Dampf einbiegen oder aus einem stärkeren Brett herausarbeiten. Da bei uns die auszuwechselnden Planken-Stücken in diesen Regionen sehr kurz waren, entschlossen wir uns für das Letztere.
Der Spiegel
Wie bei vielen alten Yachten ist der Spiegel der Logo relativ klein. Er war aus einem Eichenstück gefertigt. Das Boot hatte in den achtziger Jahren eine Edelstahl Seereling mit Bug- und Heckkorb. Der Heckkorb war mit vier Bolzen durch den Spiegel verbolzt. Feuchtigkeit drang durch die Stützen des Heckkorbes und blieb zwischen Spiegel und CFK- Beschichtung . Von innen war der Spiegel gesund, aber von außen verrottet. Mit einem Sägeblatt durchtrennten wir die eisernen Nägel und Schrauben, mit denen die Planken am Spiegel befestigt waren. Wir konnten ihn leicht ausbauen und gut als Modell verwenden. Mühsam war es, die Maße auf den neuen Spiegel zu übertragen. Auch das genaue Einpassen kostete viel Zeit.
Die Deckskonstruktion
Das Deck liegt auf einer Reihe Längs- und Querversteifungen. Die Längsverbindung wird durch die Decksplanken, Balkweger und Schlingen erreicht. Das Deck bildet einen der Hauptlängsverbände des Schiffes. Für die Querversteifung dienen die Decksbalken. An den Stellen, wo das Deck besonders beansprucht wird. verwendet man verstärkte Decksbalken, die noch zusätzlich mit Eisenknien mit den Spanten verbunden sind. Von vorn nach achtern aufgezählt befinden sich solche am vorderen Poller, neben dem Mast, vor und hinter den Aufbauten und am Leitwagen, der den Zug der Grosschot auf das Deck überträgt. Diese Decksbalken werden mit den Balkweger durch Verstärkungskniee verbunden. Dort wo Aufbauten, Luken oder das Cockpit vorhanden sind, können die Decksbalken nicht von einer zur anderen Seite durchgeführt werden. Sie sind durchschnitten und werden halbe Decksbalken genannt. Aussen liegen sie auf den Balkweger, innen stützen sie sich auf einen Unterzug oder Schlinge. Jede Schlinge erfordert an ihrem Ende zur Auflage einen verstärkten Decksbalken. Sie soll die halben Decksbalken aufnehmen und den durch den Ausschnitt in dem Deck verlorenen Längsverband wieder herstellen. Unterzüge werden auch sonst an allen Stellen verwendet, an denen starke Beanspruchungen am Deck auftreten. Wo der Ruderschaft durch das Deck geführt wird, am Leitwagen, wo Klampen und Poller sitzen. Diese Unterzüge reichen von einem zum nächsten Decksbalken und sind mit ihnen vernagelt. Die Sülle werden an den Schlingen und Decksbalken angeschraubt, ebenso wie die Seitenwände des Cockpits und der Aufbauten.
Die Decksplanken
Der äußerste Plankengang des Decks, der Schandeckel oder das Schandeck, greift über den Scheergang über. Das Schandeck ist aus festem Holz, Teak oder Mahagoni, da es einen wesentlichen Teil des Längsverbandes ausmacht und da es durch die an ihm befestigten Klampen und ähnliches besonders beansprucht wird. Oben auf dem Schandeck sitzt die Relingsleiste. Meist besteht sie aus einer aufrecht stehenden Leiste, welche oben durch eine Querleiste abgeschlossen wird. In der Mitte des Decks findet sich eine breite Decksplanke aus Teak oder Mahagoni, die Mittelfischung. Die übrigen Decksplanken waren früher meist aus leichterem Holz z.B. Whitepine, Oregonpine oder Lärche, heute verwendet man für das gesamte Deck Teakholz. Die Decksplanken werden genauso wie die Außenhautplanken gegeneinander abgedichtet, indem man sie unter aneinander anliegen lässt, nach oben zu jedoch so gearbeitet, dass ein keilförmiger Spalt zwischen ihnen bleibt, in den man Dichtmaterial (Werg, Baumwolle) hineintreibt, worüber Pech oder Marineleim gegossen wurde. Heute stehen bessere Vergussmassen wie Sika-Flex oder WKT zur Verfügung.
Bei Booten mit Leinwanddecks kann man sich das Abdichten der Planken sparen. Man darf die einzelnen Planken sehr viel schwächer wählen. Es wurden meist wesentlich breitere Planken verwendet. Die Leinwand wird mindestens l 2 Std. in klares Wasser gelegt, um die Appretur herauszuwaschen und so das Einläufen zu verhindern. Alle Unebenheiten am Deck werden geglättet (ausgespachtelt). Dann wird das Deck mit Lack oder Öl gestrichen. Nach dem Trocknen spannt man den Stoff darüber. Ist die Decksbreite größer als die Leinwand, so wird sie aus Stücken zusammengenäht Die Mittelnaht wird auf Schiff-Mitte gelegt und kann später mit einer Leiste abgedeckt werden. Die Leinwand wird von mittschiffs nach vorn und achtern sowie nach außen gespannt Falten weggezogen oder geglättet Der Stoffbezug sollte ruhig kräftig sein. Wichtig ist, dass die Decksplanken unter der Leinwand arbeiten können. Würde die Leinwand am Deck kleben bleiben, wäre sie schnell eingerissen. Entweder wird die Leinwand über das Schandeck gespannt und festgenagelt und mit der Scheuerleiste abgedeckt oder im Schandeck befestigt. Dafür wird auf der Deck zugewandten Seite ein Stück weggehobelt, um später die Leinwand und eine Abdeckleiste aufzunehmen. Steht die Kajüte bereits, wird die Leinwand an ihr festgenagelt und mit einer Viertelstableiste abgedeckt. Das Deck wird dreimal mit Vorstichfarbe gestrichen Zum Schluss wird mit einer Leinendeckfarbe gestrichen, die nicht reißt.
Die Logo bekam ein verdeckt genageltes Stabdeck: Die Mittelfischung aus Mahagoni und die Decksplanken aus Lärche. Um die Arbeiten im Achterschiff leichter ausführen zu können, entfernten wir das Achterdeck. Es bestand aus einfacher Kiefer. Das Deck war gespachtelt und mit einer Art Pappe belegt, mit GFK überzogen und zum Schluss mit Tretmaster belegt. Es gibt noch eine Reihe mehr Möglichkeiten. Z.B. ein Sperrholz Deck auf das alte zu legen Es sollte nicht zu stark sein, damit es noch der Deckswölbung angepasst werden kann, auch müssen die Kanten gut versiegelt werden. Man kann auch ein neues Stabdeck versetzt auf das alte legen. Sollten aber die Nähte nicht ganz dicht sein, so rottet das alte unter dem neuen Deck .Welche Methode man auch wählt, man sollte Sie sorgfältig ausführen und das Deck auch später gut im Auge behalten. Leckende Nähte müssen zügig erneuern werden. Denn ein Holzschiff kann ruhig etwas Wasser von unter machen, aber nicht von oben.
Das Rigg
Auf Yachten der frühen 20iger Jahre herrscht noch das Gaffel rigg vor. Aber das Hochrigg begann bereits seinen Siegeszug vorzubereiten. Zuerst bei den Regattabooten mit verleimten Peitschenmasten, die die Segelform der krummen Steilgaffel nachahmten. Kurze Zeit später wurden sie durch gerade Masten ersetzt. Die Nachteile eines Peitschenmastes waren zum einen der aufwendige Bau und somit recht hoher Preis, sowie ein schlecht stehendes gerefftes Großsegel. Es dauerte nicht lang und auch die neuen Fahrtenyachten wurden mit Hochriggs ausgestattet. Die Hauptargumente waren bessere Am -Wind - Eigenschaften und bequemere Bedienung. Ende der 20iger Jahre bekamen so gut wie alle neuen Yachten ein Hochrigg. Es setzte eine regelrechte Hochriggeuphorie ein. Viele ältere Yachten wurden ungeriggt und in neue Bootsklassen aufgenommen z.B. 8mR als 50m2 See-fahrtkreuzer, 75 m2 Nationaler Kreuzer als 50 m2 Seefahrtkreuzer, 125 m2 Nationaler Kreuzer als 80 m2 Seefahrtkreuzer usw.
Ungewöhnlich war es bei der Logo, denn sie erhielt ein Gaffelrigg mit Sloop und Yawl-Takelung von 48 m2. Von der Position des Besanmastes zeugen noch seine Püttinge und die große Anzahl Spanten und Bodenwrangen im Heckbereich. Leider haben wir keinen Segelriss der Logo. Aber es existieren einige Segelrisse von vergleichbaren Booten in Aussehen und Größe, die im selben Zeitraum bei Burmester entstanden und ebenfalls von Arthur Tiller konstruiert wurden. Ein Segelriss einer l0-m Fahrtenyacht von 1924 ist abgebildet. Die Logo soll wieder als Sloop mit Steilgaffel getakelt werden.
Zum Bau von Rundhölzern eignet sich Fichte, Tanne - besser Spruce oder Oregon-Pine. Das Holz sollte möglichst feinädrig und astrein sein. Die stärkste Stelle des Mastes soll sich dort befinden, wo die größten Kräfte auftreten - etwa auf zwei Drittel der Länge zwischen Deck und Gaffelklau. Die Wandung hohler Masten muss mind. 1/5 D betragen. Bei Bäumen und Gaffel ist die stärkste Stelle in der Mitte.
|
|